From the New Norm to a New Future: Ensuring Business Continuity
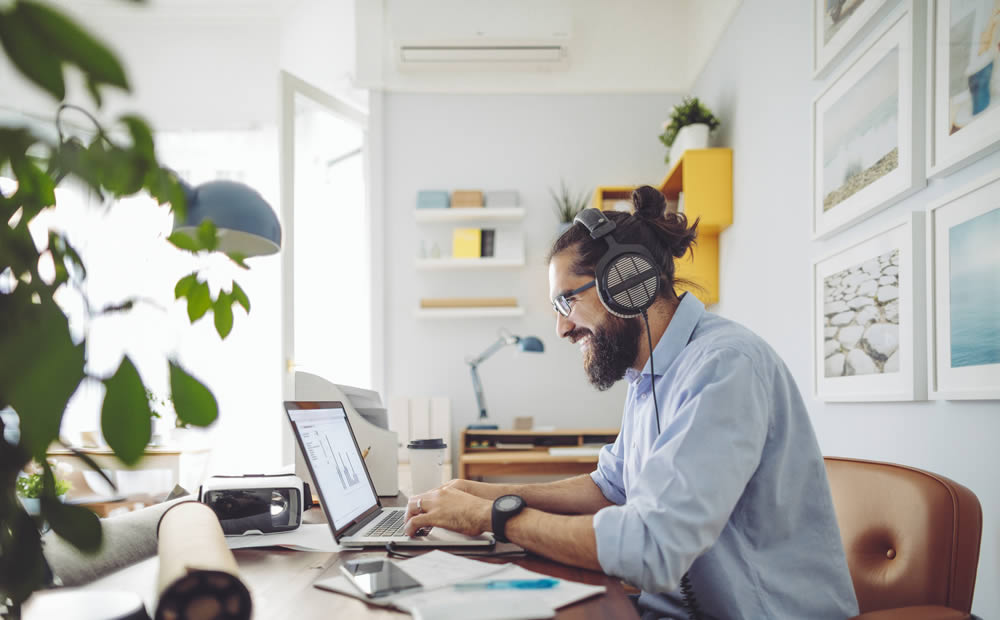
There’s no doubt that 2020 had a huge impact on societies around the globe, changing how we live, work and conduct business. Data centers had to quickly respond as the COVID-19 pandemic forced businesses to shift to remote working and provide some semblance of “business as usual” via online collaboration, virtual events, enhanced e-commerce and digital customer services.
As a managed service provider, you’re not alone if your customers’ sudden need for increased bandwidth, VPN usage and cloud-based platforms had you scrambling to expand capacity, while still delivering assured availability. This reactive approach put massive pressure on existing data center infrastructure, but what may have seemed like a messy, temporary band aid at the onset of the pandemic is now a reality for the foreseeable future. It’s become increasingly evident that we’ve transitioned into a “new norm” with many businesses continuing to expedite their digital transformation plans and showing no signs of slowing down.
Successfully maintaining business continuity in 2021 and beyond places newfound emphasis on the need for your data center infrastructure to ensure low-latency performance, maximize reliability while enabling rapid deployment and scalability. This demands a forward-thinking approach to ensure you have an optimized DC design in place with the right architecture, topology and components to support you for the long term.
Navigating a Complex Landscape
When it comes to taking a step back from impromptu, improvised response in your data center and focusing on long-term digital transformation and business continuity, there are several considerations to keep in mind as you navigate the complex landscape of design and deployment options.
Hyperconverged infrastructure technologies and techniques adopted by the likes of Google, Microsoft and other large hyperscale data centers are no longer out of reach for your data center thanks to advanced open-source protocols, white-box hardware and software-defined networking. These high-density, highly virtualized server environments are ideal for enabling the cost-effective expansion and scalability you need to support your customers’ digital transformation.
But with virtual environments distributing resources across multiple servers located anywhere in the data center, dynamic server-to-server communication demands low latency, high-bandwidth transmission. This requires taking a closer look at your architecture and topologies and choosing a design that reduces the number of switches that data must traverse, enabling more east-west traffic between servers rather than north-south traffic through multiple tiers of switches. It also means determining where to locate equipment and how to connect it to best meet your current and future manageability, flexibility, scalability and security needs.
At the same time, innovations in switching technology have established an easier migration path to 25, 50 and 100 Gb/s speeds in switch-to-server connections with 100, 200 and 400 Gb/s speeds in backbone links. There are now more options than ever for supporting these speeds-from twinax Direct Attach Cable (DAC) assemblies and Active Optical Cables (AOCs) for direct equipment-to-equipment links, to multiple Multimode and Singlemode fiber applications using parallel optics with multi-fiber connectivity (i.e., MPO/MTP) or wave division multiplexing (WDM) technologies. With a range of distance capabilities, power consumption, performance, and material and installation costs, it can be difficult to navigate the options and know which solution provides the right combination of cost, performance, reliability and scalability to best meet your MSP model and budget.
Therefore, Trusted Guidance is Essential
As technology continues to evolve and digital transformation ramps up with the new norm that has become the new future, managed services will continue to be critical for supporting business needs across all market sectors. As a managed service provider, you need to be ready to support your customers and set yourself up for a successful 2021 and beyond.
When it comes to designing and deploying data center infrastructure for business continuity, you need a partner with the expertise, end-to-end solutions and associated services to ensure you can effectively and quickly expand your available services no matter what comes your way without jeopardizing your operational performance.
With value-added Data Center Design Services and a full range of high performance fiber, high speed interconnects and copper systems to support 10 to 400 Gigabit applications and beyond, Siemon can ensure:
- Worry-free infrastructure – via non-blocking, low-latency architecture and topologies that support emerging technologies and effective hyperconverged environments.
- High-density, flexible solutions – that ease expansion while ensuring manageability, security and compliance.
- Reduced complexity, risk and costs – with consistent beyond-standards performance and quality across all systems, regardless of the application.
Backed by industry leadership, renowned technical service, a strong data center partner ecosystem and excellent supply chain logistics, Siemon doesn’t just help you design and deploy data center infrastructure for today, our experienced teams work with you to design, implement and deliver a high quality infrastructure approach backed by a comprehensive service offerings that prepare you for the challenges ahead.
Learn more about how Siemon can help you maintain business continuity in 2021 and beyond.
Other recent blogs we think you’ll like: